Molding Plastic: Transforming Industries with Precision and Innovation
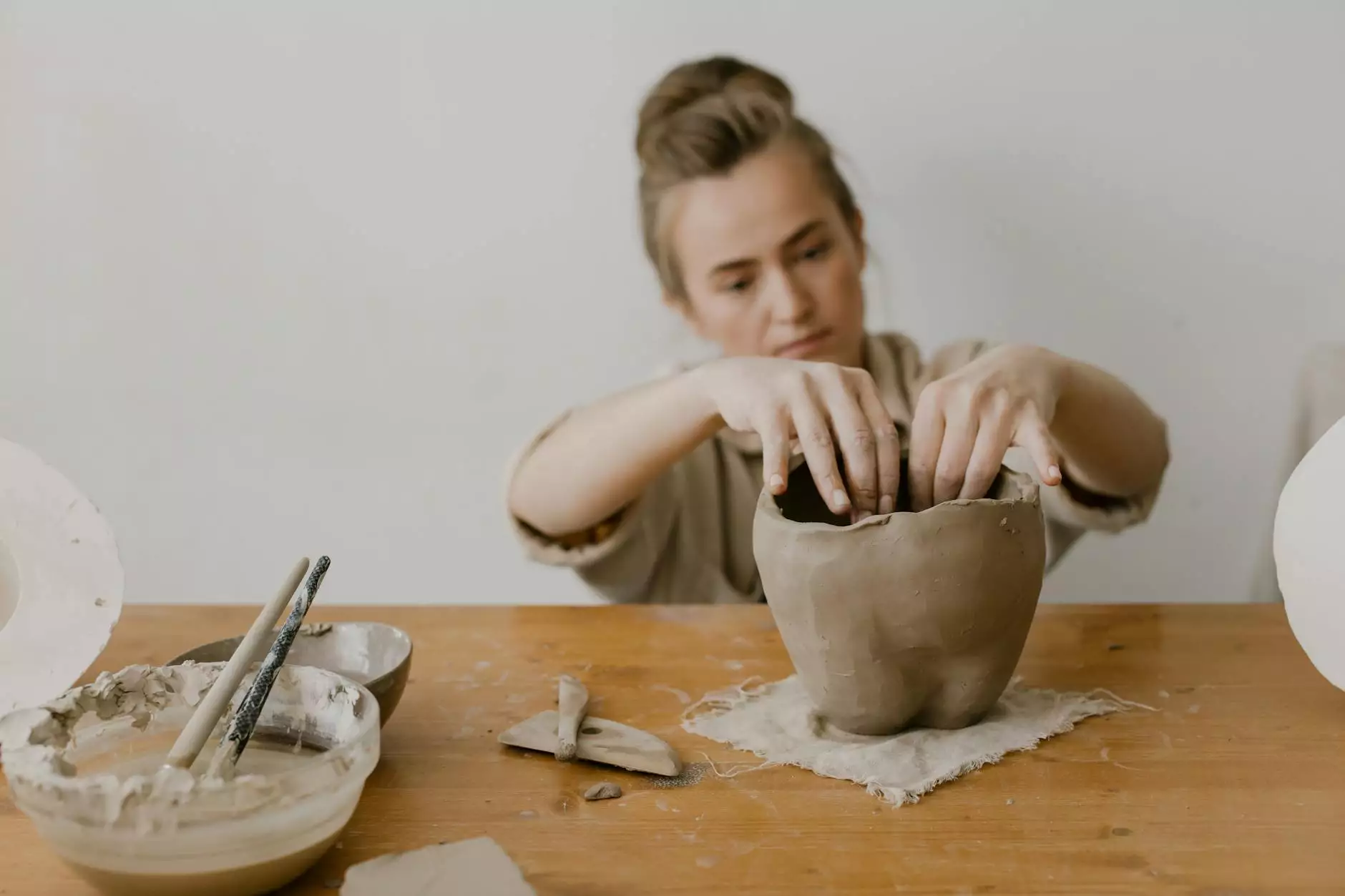
Molding plastic has emerged as a pivotal technique in modern manufacturing, allowing companies across various industries to produce intricate and durable products. From automotive components to consumer goods, the significance of plastic molding is undeniable.
Understanding Molding Plastic
Molding plastic involves shaping molten plastic into specific forms using molds. This technique is favored for its efficiency and flexibility, making it ideal for mass production. The process of molding plastic can be categorized into different types, notably:
- Injection Molding: A widely used process where plastic is injected into a mold. This method is popular for producing high volumes of components with high precision.
- Blow Molding: This technique is primarily used for creating hollow plastic objects, such as bottles and containers.
- Rotational Molding: In this process, plastic is heated and gradually rotated within a mold, useful for creating larger, more complex shapes.
- Compression Molding: Used typically for thermosetting plastics, this process involves placing plastic in a heated mold and applying pressure.
The Benefits of Molding Plastic
The advantages of using molding plastic in manufacturing are manifold:
- Cost-Effectiveness: Molding plastic allows for high-volume production at a lower per-unit cost, making it economically viable for manufacturers.
- Design Flexibility: The ability to create complex shapes and designs enables innovation without substantial increases in manufacturing costs.
- Durability: Finished plastic products are often lightweight yet durable, providing longevity in various applications.
- Environmentally Friendly Options: Advances in technology have led to the development of biodegradable and recyclable plastics, making molding processes more sustainable.
Applications of Molding Plastic in Various Industries
Molding plastic has various applications across multiple sectors, showcasing its versatility:
1. Automotive Industry
The automotive sector relies heavily on molding plastic for creating parts such as dashboards, panels, and bumpers. The lightweight nature of plastic not only reduces vehicle weight but also contributes to fuel efficiency.
2. Consumer Goods
From household items to electronics, molded plastic components are everywhere. The ability to produce items in bulk with intricate designs makes it ideal for consumer products like packaging, toys, and kitchenware.
3. Medical Field
In healthcare, molding plastic is critical for producing medical devices, disposable instruments, and packaging that meet stringent sanitary standards. The capacity to create biocompatible materials ensures safety in medical applications.
4. Construction Industry
With the rise of sustainable building materials, plastic molded products are increasingly used in construction for piping, insulation, and other components that require durability and resistance to environmental factors.
Innovations in Molding Plastic
Over the years, innovations in molding plastic technology have dramatically improved efficiency and opened new possibilities. Some notable advancements include:
- 3D Printing Integration: The integration of 3D printing with traditional molding techniques allows for rapid prototyping and development of complex geometries.
- Smart Plastics: Incorporating sensors into molded plastic items enables the creation of smart products for various applications, including consumer electronics and healthcare.
- Recycling Technologies: Advances in recycling processes have led to the development of methods to reclaim and reuse molded plastics, enhancing sustainability across industries.
The Future of Molding Plastic
The future of molding plastic looks promising, driven by technological advancements and increasing demand for sustainable practices. Some trends to watch include:
- Enhanced Automation: The incorporation of automation and robotics in the molding process will streamline operations and reduce manufacturing times.
- Focus on Sustainability: There will be an emphasis on using recycled materials and developing new biodegradable plastics to meet environmental goals.
- Customization: With advancements in technology, more tailored and customizable molding options will emerge to meet specific client needs.
Conclusion
In conclusion, molding plastic is an essential process that plays a crucial role in modern manufacturing. Its benefits span across various industries, making it a key player in the global economy. As technology continues to advance, the possibilities for plastic molding are limitless, paving the way for innovative designs and sustainable practices.
For businesses looking to invest in molding plastic solutions, partnering with experts such as DeepMould.net can provide invaluable insights and quality services that align with the latest industry standards. Embrace the future of manufacturing with molding plastic!