Understanding Lift Station Back-Up Monitors: A Comprehensive Guide
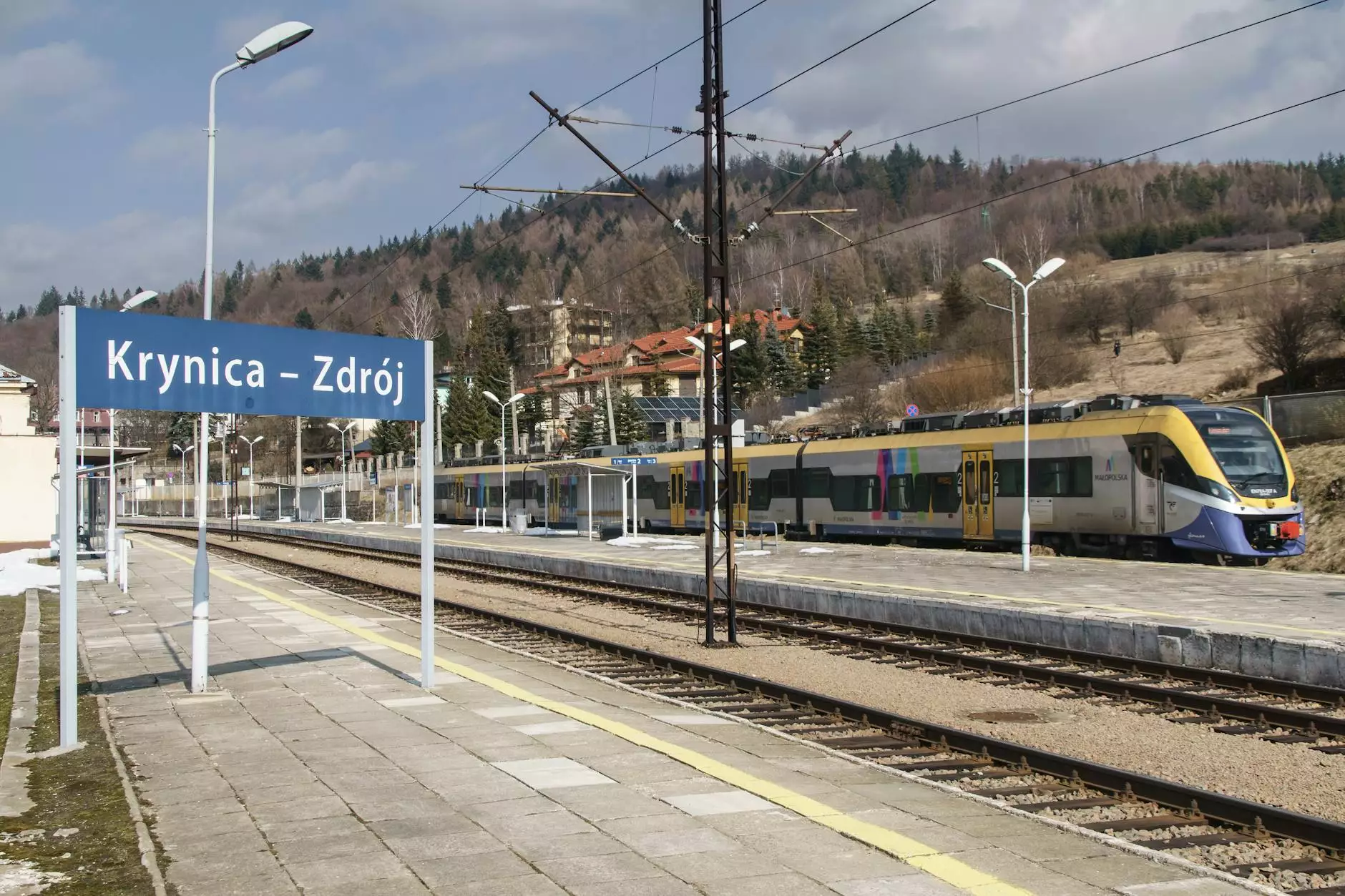
Lift station back-up monitors play a critical role in the management and operation of sewage systems, stormwater management, and various industrial processes. Their presence not only enhances safety but also ensures uninterrupted service, ultimately protecting the environment and public health. This article delves into the functionalities, benefits, and crucial features of these indispensable devices, ensuring you have all the information necessary to make informed decisions about your sewage and drainage systems.
What is a Lift Station Back-Up Monitor?
A lift station back-up monitor is a sophisticated sensor and alert system designed to monitor the performance and operational status of sewage lift stations automatically. Primarily, these monitors are vital for ensuring continuous operation, minimizing downtime, and providing real-time data regarding pump performance.
The Functionality of Lift Station Back-Up Monitors
These monitors operate by tracking numerous parameters essential to the functioning of a lift station:
- Fluid Level Monitoring: Detects the fluid levels within pumps and tanks to prevent overflow.
- Pump Performance Tracking: Monitors the operational efficiency of pumps, ensuring they run within optimal parameters.
- Alarm Systems: Provides alerts for malfunctions or performance issues, allowing swift action to avoid environmental hazards.
- Remote Access: Many systems allow operators to access performance data and alerts remotely, enhancing operational flexibility.
Why Your Business Needs a Lift Station Back-Up Monitor
Integrating a lift station back-up monitor into your waste management strategy is essential for several reasons:
1. Enhanced Operational Efficiency
Boosting operational efficiency is paramount in any business. Back-up monitors provide real-time insights that help in optimizing day-to-day operations. Proprietors are informed instantly of any irregularities, allowing for quick responses.
2. Prevention of Environmental Hazards
Failing to monitor lift stations can lead to catastrophic failures, invariably resulting in environmental incidents. A poor pump performance can cause sewage overflows, which carry significant legal and cleanup costs. Implementing a back-up monitor minimizes these risks by continuously tracking operational metrics.
3. Cost Efficiency
Investing in a reliable lift station back-up monitor can mitigate hefty repair costs that arise from unexpected breakdowns. By detecting issues early, businesses can schedule maintenance proactively, avoiding costly emergency repairs.
4. Regulatory Compliance
With environmental regulations tightening globally, adopting a monitoring solution is no longer optional—it’s a necessity. Many jurisdictions require specific standards for wastewater management, and having a monitoring system actively supports compliance with these regulations.
Key Features to Look for in a Lift Station Back-Up Monitor
When selecting a lift station back-up monitor, it is crucial to consider several features to ensure you invest in a quality product:
1. Real-Time Monitoring
The ability to receive immediate alerts about fluid levels, pump status, or any abnormalities is invaluable. Real-time data ensures that operators can handle issues as they arise, providing a proactive approach to management.
2. User-Friendly Interface
An intuitive design makes it easier for operators to interpret data. Look for monitors with straightforward dashboards and mobile accessibility features that simplify monitoring from any location.
3. Durability and Weather Resistance
Lift stations are often subjected to harsh conditions. Choosing a back-up monitor constructed from durable materials, resistant to water, dust, and other environmental factors, ensures longevity and reliability under tough operational circumstances.
4. Comprehensive Reporting
Monitors that provide detailed reporting can help operators analyze trends over time, allowing for more strategic maintenance scheduling and upgrades.
5. Integration Capabilities
Ensure that the monitor can easily integrate with existing systems and software used by your business. This ensures seamless communication between devices and better data management.
Installation and Maintenance of Lift Station Back-Up Monitors
Installing a lift station back-up monitor is an essential process that should be completed by certified professionals. Proper installation guarantees its functionality and reliability across all operational scenarios. Here’s a quick overview:
Installation Process
- Site Assessment: Conduct a thorough evaluation of the lift station to determine the best location for the monitor.
- Configuration: Configure the monitor settings, ensuring alignment with operational requirements.
- Testing: Perform rigorous tests to confirm the system operates as expected before going live.
Regular Maintenance Routines
Once installed, maintaining the monitor is crucial for optimal performance. Regular inspections and updates should include:
- Inspection of sensor functionality.
- Clearing any debris or blockages.
- Software updates to enhance performance and introduce new features.
Case Studies: Success Stories of Lift Station Back-Up Monitors
Numerous organizations have seen transformative benefits by implementing lift station back-up monitors. Here are a couple of examples:
Case Study 1: Urban Sewage Management
A major urban area faced regular issues with pump failures, leading to sewage overflow incidents. By installing comprehensive lift station back-up monitors, the management team significantly reduced failure rates. With real-time monitoring and predictive maintenance patterns, the average response time to issues decreased by over 40%, leading to improved public health and satisfaction.
Case Study 2: Industrial Facility
An industrial facility dealing with wastewater needed to comply with strict environmental standards. After implementing a back-up monitoring system, they not only met compliance but also enhanced their operational efficiency. The facility reported a 30% reduction in maintenance costs within the first year, showcasing the cost-benefit of investing in these advanced systems.
Conclusion
A lift station back-up monitor is more than just a safety tool; it is a robust and strategic asset in managing wastewater systems. The balance of operational efficiency, environmental responsibility, and cost-effectiveness makes it a necessary investment for businesses in various sectors.
As industries continue to evolve and face new challenges, ensuring the reliability of lift stations with advanced monitoring solutions is essential for survival and success. If you're considering upgrading your lift station’s monitoring systems, explore the offerings at tankvitals.com to find the perfect solution tailored to your business needs.
FAQs about Lift Station Back-Up Monitors
1. How often should I check my lift station back-up monitor?
While these systems are designed for real-time monitoring, it’s advisable to perform manual checks and maintenance at least once every quarter.
2. Can I integrate a new lift station back-up monitor with existing systems?
Most modern systems are designed to integrate easily. Always check for compatibility with your current infrastructure before purchasing.
3. What should I do if my monitor alerts me of an issue?
Immediately assess the situation. If you're trained, perform necessary troubleshooting; otherwise, contact a professional technician promptly.
4. Are there additional features that I should consider?
Besides real-time monitoring and alerts, consider features such as predictive analytics that can forecast potential failures before they occur.
5. Can lift station back-up monitors reduce operational costs?
Yes, by improving efficiency and reducing downtime, they often lead to lower maintenance and repair costs long-term.
Discover more about enhancing your lift station operations and ensuring reliability in your water management solutions by visiting tankvitals.com. Equip your business with the right tools for success!